IoT Applications
Where IoT Can Improve Beer Production Processes?
Views : 5401
Author : Fiona Dai
Update time : 2023-10-16 11:24:21
In the beer production process there are manufacturing malt, crushing raw materials, saccharification, fermentation, storage and maturation, filtration, filling and packaging and other processes. Need to use the wind separator, sieving machine, saccharification pot, fermentation equipment, filtration machine, filling machine, packaging machine and other food machinery and equipment. The automation and intelligence of these food machinery and equipment together promote the automated production of beer.
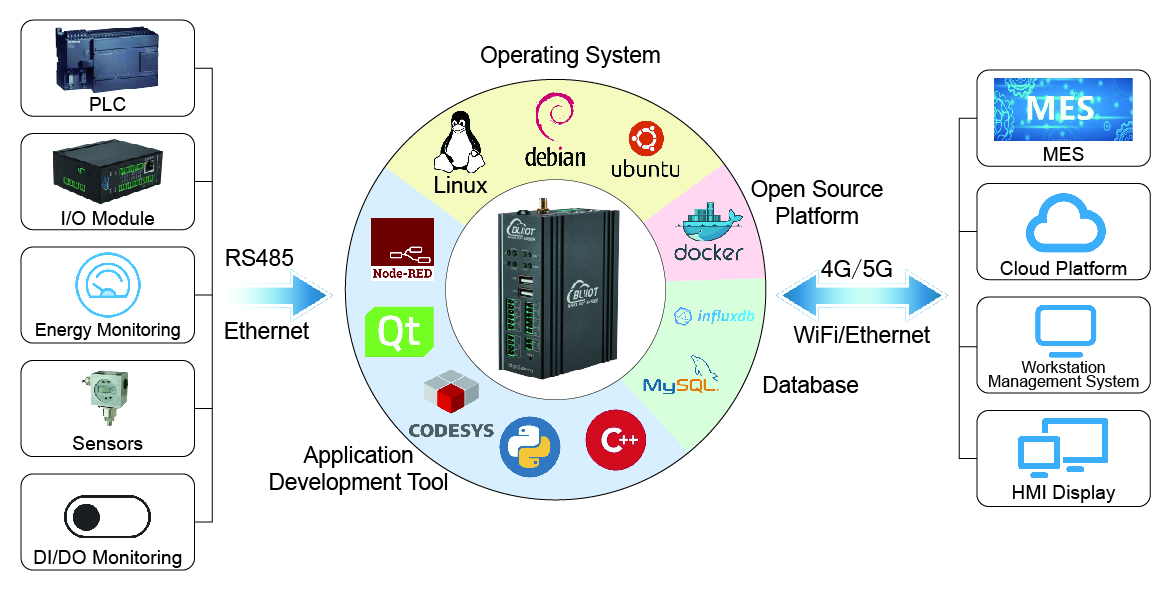
Use BLIIoT EdgeCOM to monitor each production process on the production line; and connect PLC to the EdgeCOM, so that you can not only check the data on HMI, at the same time, the data can be uploaded to the OPC UA client(MES, DCS, etc.).
PLC receives and processes sensor data, controls equipment hydraulic, pneumatic, electrical parameters, etc., while BLIIoT EdgeCOM responsible for controlling the entire production process, to achieve the purpose of information interoperability.
2, Write a program through Node-RED or QT to get the data to be displayed from the device, and finally display the data in charts, lists, or other forms on the corresponding interface.
3, Transfers data to enterprise management systems such as MES.
Advantage of EdgeCOM
1, Support a variety of communication protocols, reducing communication costs.
2, EdgeCOM collect the operation status, sensing data, recipe data and alarm information of the equipment, and judge whether it meets the production requirements, according to the analysis results, the EdgeCOM sends control instructions to PLC through OPC UA, then PLC drives the mechanical arm and conveyor belt and other equipment to execute the corresponding actions.
3, Real-time recording of production line data (e.g., sensor readings, control commands, and product classification), which can be uploaded to My SQL databases, enterprise-level MES, DCS, SCADA, etc., or cloud-based platforms for further analysis.
4, Support LINUX, Ubuntu, Debian, and other OS, and support Node-Red, QT, Python, C++ and other application programs. Users can program it by themselves according to their needs.
4, Supports remote configuration and remote upgrade.
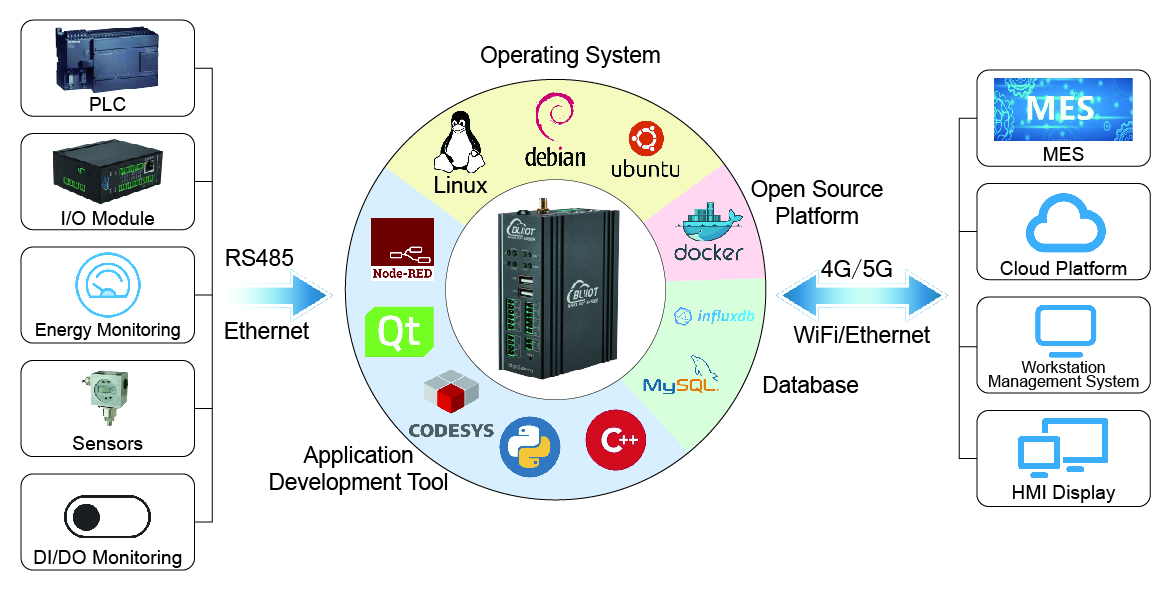
Use BLIIoT EdgeCOM to monitor each production process on the production line; and connect PLC to the EdgeCOM, so that you can not only check the data on HMI, at the same time, the data can be uploaded to the OPC UA client(MES, DCS, etc.).
PLC receives and processes sensor data, controls equipment hydraulic, pneumatic, electrical parameters, etc., while BLIIoT EdgeCOM responsible for controlling the entire production process, to achieve the purpose of information interoperability.
What EdgeCOM implements in the system?
1, Control commands are sent to the PLC by analyzing the data collected by the PLC.2, Write a program through Node-RED or QT to get the data to be displayed from the device, and finally display the data in charts, lists, or other forms on the corresponding interface.
3, Transfers data to enterprise management systems such as MES.
Advantage of EdgeCOM
1, Support a variety of communication protocols, reducing communication costs.
2, EdgeCOM collect the operation status, sensing data, recipe data and alarm information of the equipment, and judge whether it meets the production requirements, according to the analysis results, the EdgeCOM sends control instructions to PLC through OPC UA, then PLC drives the mechanical arm and conveyor belt and other equipment to execute the corresponding actions.
3, Real-time recording of production line data (e.g., sensor readings, control commands, and product classification), which can be uploaded to My SQL databases, enterprise-level MES, DCS, SCADA, etc., or cloud-based platforms for further analysis.
4, Support LINUX, Ubuntu, Debian, and other OS, and support Node-Red, QT, Python, C++ and other application programs. Users can program it by themselves according to their needs.
4, Supports remote configuration and remote upgrade.
Related News
Read More >>